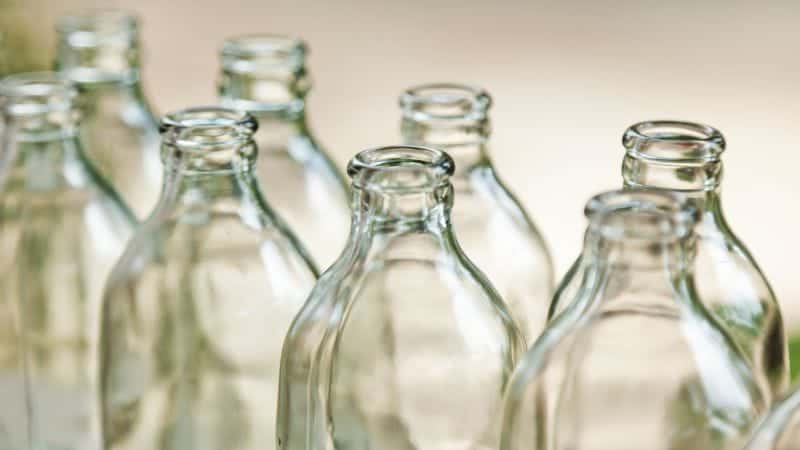
The finish of a bottle is the part that connects the neck to the body. It plays an important role in how easily a bottle can be opened, closed, and poured from. The finish determines which type of closure a bottle requires, such as a cork, cap, or other sealing method. There are several common bottle finish styles used in the beverage and packaging industries. This article will explore the most popular bottle finish types, their key features, and common applications.
Bottle Finish Fundamentals
When you’re exploring the world of bottles, understanding the top part of the bottle, commonly referred to as the finish, is crucial. This section will give you insight into what a bottle finish is and the different styles that exist.
Defining Bottle Finishes
A bottle finish, or sometimes simply called a “finish,” specifically refers to the feature of the bottle that provides a means for sealing. This includes the lip, collar, and the closure system, ensuring the contents remain within the bottle until intended use. The finish is an essential component since it directly interacts with various closure mechanisms, whether the bottle is designed to be sealed just once or is returnable for multiple uses.
- Mouth-blown Bottles: Typically feature simple finishes such as rolled or folded edges.
- Machine-made Bottles: Often utilize complex thread finishes.
Historical Context and Evolution
When you explore the history of bottle finishes, you enter a world where techniques and styles reflect the broader technological advancements of their times.
You can trace the bottle dating back to characteristics such as the finish—the lip at the bottle’s opening. Early finishes were quite simple. For example, the cracked-off finish, common until the 1850s, left a rough edge that was the result of glassblowing techniques before the lip of the bottle was refined. Moving from simple to sophisticated, you have the goffering finish, noted in an 1886 U.S. Patent Office document, showcasing a period when manual craftsmanship was still paramount in bottle making.
A heavy, rounded ring known as the cap-seat finish emerged, with a ledge below the lip to secure a cap. This design, detailed in a 1947 Owens-Illinois drawing, signifies a shift to more precise and functional bottle finishing methods.
Styles and Types of Finishes
Finishes have evolved to accommodate different closures and uses. Here’s a quick guide to help you identify some of the common styles:
- Thread Finish: Characterized by the presence of continuous threads that spiral around the bottle neck, designed to engage with a screw-cap.
- Rolled Finish: A method where the glass at the open end of the bottle is rolled outward, sometimes inward, and downward.
- Flare Finish: The glass flares outward, creating a distinct difference in diameter between the neck and the opening.
It’s important to note that the design and method of finishing can dictate the type of closure appropriate for a specific bottle, ensuring the contents are secured and preserved correctly.
Understanding these fundamental concepts allows you to better select and use bottles for your needs, whether for personal projects or commercial packaging.
Key Measurements and Dimensions

When selecting the perfect bottle closure, you should consider several crucial measurements to ensure a secure fit.
Understanding Bottle Measurements
Neck Finish: This is the term for the specifications of the bottle’s opening. It’s important to measure the diameter of the outermost threads – this figure represents the “T” dimension of your container.
- “T” Dimension: The outer diameter of the thread. This is measured in millimeters (mm).
- “I” Dimension: The inner diameter of the bottleneck. It’s critical as it determines the size of the closure that will fit.
Common Finish Measurements
Bottleneck finishes are often represented by two figures, indicating the type of threads and dimensions. For example:
- 24mm T dimension with 1.5 thread turns may be described as 24/410 neck finish.
- Similarly, a 28mm T dimension with different thread turns might be a 28/415, 28/400, or 28/425 finish.
Thread: This refers to the helical structure that enables the cap to screw onto the bottle. The thread count and size often determine the “H” dimension—the height from the top of the finish to the point where it intersects with the shoulder of the bottle.
Thread and Closure Design
Understanding the thread mechanisms and closure design of bottle finishes is crucial for selecting the right packaging for your product. Let’s explore the specific functions of threads and how they interact with closures to create a secure seal.
Thread Mechanisms and Functions
Thread Mechanisms are the heart of a bottle’s neck finish, determining how your cap will attach and secure itself.
- Continuous Thread (CT): A continuous spiral that allows the cap to screw on with multiple turns.
- Thread Turn & Engagement: Indicates how many times a cap will twist before it is fully sealed. Thread engagement refers to the depth and fit between the cap’s threads and the bottle’s neck finish.
- GPI Standard: A common system used to standardize thread styles, denoting thread turns with a dash number (e.g., a 400 GPI finish indicates a single thread turn).
Functionality: You’ll find that the thread mechanisms govern the application torque, the effort needed to close or open the cap, and play a vital role in the product’s integrity and user experience.
Closure Types and Compatibility
Your closure type must complement the thread style of your bottle’s neck finish to function properly.
- Types of Closures:
- Caps: Match the inner threads of the cap with the bottle’s outer threads.
- Rings & Seals: Often found on tamper-evident and child-resistant closures.
Compatibility:
- Mating: A proper fit between the cap and neck finish ensures a tight seal, efficient use, and safety of contents.
- Cap & Neck Matching: Refer to GPI/SPI standards for matching cap sizes to neck finishes—such as a 410 GPI cap for a bottle with 1.5 thread turns.
When selecting your closure, consider the thread depth and thread turn to ensure it will securely mate with your bottle’s neck finish. Look for numbers like 415 (2 narrow thread turns) or 425 (buttress finish with thick threads), which describe the thread style and the degree of thread engagement required for the closure to perform optimally.
Material Considerations for Bottle Finishes

When selecting the finish for your bottle, it’s essential to consider the material it’s made from. Your choice will affect not only the aesthetics but also the functionality and compatibility with different caps or closures. Here’s a closer look at glass and plastic bottle finishes.
Glass Bottle Finishes
Glass bottles are widely appreciated in the packaging industry for their clarity, premium feel, and recyclability. The Glass Packaging Institute (GPI) sets standards for glass bottle finishes to ensure industry-wide compatibility with closures. The shape of the glass bottle’s neck and its finish must precisely match the cap or closure, which can be metal or plastic, to provide a secure seal.
Common Types of Glass Finishes:
- Crown Finish: Often used for beer bottles and soda bottles, requiring a specialized metal crown cap.
- Lug Finish: Features multiple threads for a tight seal with less rotation; perfect for pickles or sauces.
- Material Impacts: The durability of glass allows for finishes that can withstand carbonation pressure, making them ideal for sodas and sparkling wines. Moreover, certain types of finishes might require additional treatment, such as annealing, to ensure they do not crack or break under stress.
Plastic Finish Options
In the plastic packaging sector, flexibility and cost-effectiveness are the key advantages. You can find a variety of closure options suited to plastic bottles, ranging from simple snap tops to sophisticated dispensing systems. The manufacturing process for plastic bottle finishes often includes injection molding, allowing for precision and mass production.
- Different Plastic Finish Types:
- Screw caps: Easy to use and provide a reliable seal, suitable for a wide range of products.
- Flip-top caps: Convenient for dispensing liquid products like shampoos or sauces.
- Child-resistant caps: A safety feature for products that may be harmful to children if ingested.
- Considerations for Plastic: Ensure that the type of plastic used is compatible with the product it will contain to avoid degradation or contamination. The recyclability of the plastic finish is another factor to consider, aligning with environmental concerns within the packaging industry.
Industrial Standards and Guidelines
When you’re in the market for bottle packaging, it’s crucial to understand the industrial standards and guidelines. These ensure that your bottle finishes are consistent, measure properly, and secure safely with closures.
Measurement Standards
To determine the correct closure for your container, you adhere to established measurement standards. These standards describe how the neck finish of a container is measured. The Glass Packaging Institute (GPI) and the Society of the Plastics Industry (SPI) have developed scale measures that are widely adopted in the United States and Europe. For a bottle’s thread, the measurement involves:
- The “T” dimension: The outside diameter of the thread.
- The “I” dimension: The inner diameter of the bottleneck. Specifications for this dimension are critical for matching the closure to the bottle.
- The “S” dimension: Measured from the top of the finish to the top edge of the first thread. It determines the orientation of the closure to the bottle and the amount of thread engagement between the bottle and the cap.
Complying with these standards helps manufacturers produce bottles and caps that fit universally, eliminating the guesswork in the packaging process.
Manufacturing Guidelines
Manufacturing guidelines are vital for creating a secure bottle finish. Your bottle manufacturer may employ an automatic bottle machine (ABM), which shapes bottles according to precise measurements and uniform standards. Guidelines such as the ISBT Threadspecs® focus on the beverage industry and provide voluntary finish guidelines. These are:
- Thread Turn: How many times the threads pass each other to create a non-interrupted spiral.
- Thread Size: The dimension and pitch of the thread which play a critical role in the capping process.
Manufacturers often keep specific cap dimensions and additional specifications proprietary. However, by following general guidelines, caps and bottles can be designed to secure snugly and safely, avoiding product spills or contamination. Always check with your bottle finish manufacturer for specific guidelines, which references can include bodies like the Bureau of Land Management for environmental compliance.
Practical Applications and Usage
In the world of packaging, the bottle finish is paramount to maintaining the quality and integrity of the product inside. You’ll find that precise specifications for bottle finishes are critical, especially when considering factors like sealing performance and interaction with filling machinery.
Beverage Industry Standards
When it comes to beverages, the standard of your bottle finish ensures a tight seal to maintain carbonation pressure and prevent leakage. For example, soft drink and beer manufacturers typically use a crown cap finish, which involves a flange. This flange interacts with a metal cap lined with a sealing material. Pressure from the carbonation reinforces the seal, helping to keep your drink fizzy and fresh. In terms of dimensions, the inside diameter of a typical crown finish is about 26 millimeters.
For water and juice bottles, a screw cap finish is often the norm, usually showing a taper to the inner wall that aligns with the threads of the cap. This setup allows screw caps to efficiently seal liquids inside. An automatic bottle filling system will fill these bottles with minimal contact, utilizing filling tubes that align with the finish to reduce spillage.
Packaging for Sauces and Other Liquids
For sauces and condiments, the bottle finishes are particularly designed to control the flow of the product. Ketchup and mustard bottles usually employ a packer finish with a relatively wide mouth for easy dispensing. The plate at the opening may include a taper, guiding the sauce right onto your food without making a mess. Similarly, hot sauce bottles might have narrower finishes to regulate the amount dispensed.
Ink bottles, on the other hand, incorporate a bead on the opposite side of the finish, designed to wipe excess ink from the pen or dropper. This practical design ensures a clean usage experience and prevents ink from staining the bottle’s exterior.
For all these containers, specific measurements in millimeters are used for the inner wall of the finishes to ensure that lids and caps fit securely, reducing the risk of spillage and preserving the integrity of the liquids within.
In summary, the bottle finish is a crucial but often overlooked design element. It impacts the user experience with a bottle as well as which closure system can be used. While simple in appearance, the finish style chosen can have ramifications for production costs, product shelf life, and consumer convenience. With the growing demand for innovative packaging solutions, bottle finishes will continue to evolve alongside trends in materials, sustainability, and new product formulations. A well-designed finish is key to creating an optimal user experience from opening to disposal.