Plastic resins are versatile and widely used in manufacturing, packaging, and countless other applications. As the backbone of the plastics industry, understanding the different types of plastic resins is essential to grasp their various uses, properties, and potential impacts on the environment.
This article will delve into the five main categories of plastic resins and their diverse applications, like making soft drink bottles. Polyethylene, polypropylene, polyethylene terephthalate, polyvinyl chloride, and polystyrene are just a few of the most common plastic resins, each with unique properties and uses.
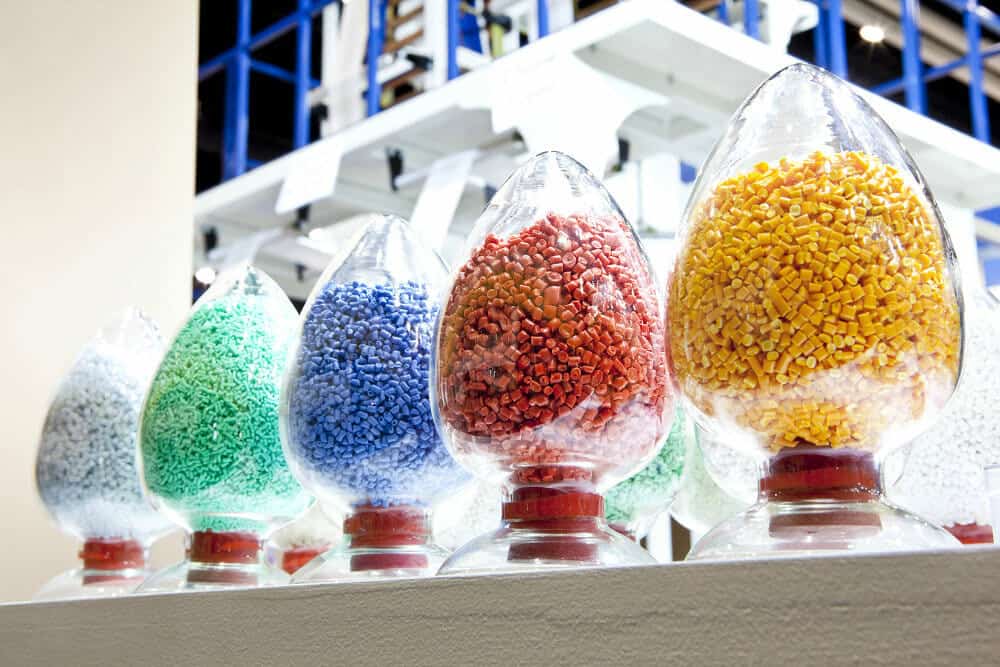
From food packaging to automotive components, plastic resin pellets play an enormous role in daily life. Additionally, environmental and recycling considerations, emerging innovations, and future developments in the field are crucial topics in understanding the broader impacts of plastic resins.
Key Takeaways
- Various plastic resins have unique properties and applications, and each has its own resin identification code.
- Recycling and environmental factors play a crucial role in plastic resin use.
- Innovations and future developments in the industry have significant impacts.
Overview of Plastic Resin Types
In your exploration of plastic resin types, it’s essential to consider both synthetic and naturally occurring resins. These materials play a crucial role in various industries for their unique properties, such as strength, flexibility, and resistance to impact. Let’s dive into some common types of plastic resins.
Polyethylene (PE), including High-Density Polyethylene (HDPE) and Low-Density Polyethylene (LDPE), is the most widely used plastic resin. You’ll find it in food plastic packaging, bottles, and grocery bags. It offers excellent resistance to chemicals and moisture, making it an ideal choice in packaging applications.
Polypropylene (PP) shares many characteristics with polyethylene; however, it has a higher melting point, which makes it suitable for use in applications requiring higher temperature resistance. This resin is commonly found in microwave-safe food containers, automotive parts, and carpet fibers.
Polyvinyl Chloride (PVC) is a popular and versatile plastic resin known for its stability, durability, and resistance to fire. You’ll find PVC in pipes, windows, and vinyl flooring applications.
Polyethylene Terephthalate (PET) is a clear and strong plastic resin for food and beverage packaging. You might recognize it as the material in plastic bottles and food trays. Its properties include excellent chemical resistance and a low gas permeability, which helps preserve the products’ freshness.
Polystyrene (PS) is another widely used plastic resin in various forms, including rigid and foam. You’ll find it in disposable cutlery, yogurt cups, and insulation materials.
Polymethyl Methacrylate (PMMA), or acrylic or Plexiglas, is a transparent and lightweight resin often used as a glass substitute. Its durable and shatter-resistant nature makes it perfect for applications like window panes and protective screens.
Apart from these synthetic resins, there are also naturally occurring resins like shellac, amber, and rosin. These substances, derived from plants and insects, possess adhesive qualities and can be used in products like varnishes and sealing waxes.
Now that you have a general idea of the various plastic resin types, you can confidently navigate through the world of plastics and their applications.
Remember, each type has unique characteristics, making it suitable for different uses. Considering these properties to make informed material selections for your projects is crucial.
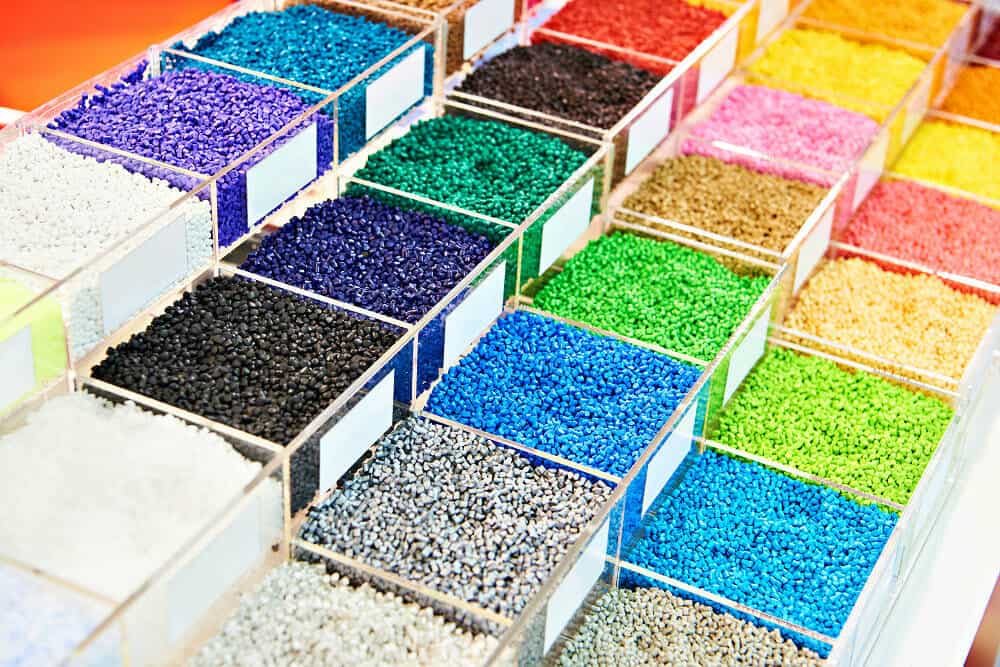
- Polyethylene
Polyethylene is the most commonly produced plastic used for packaging applications such as plastic bags, plastic films, geomembranes, and containers like bottles. In this section, you’ll learn about two main types of polyethylene: high-density polyethylene (HDPE) and low-density polyethylene (LDPE).
- Polypropylene
Let’s talk about polypropylene, a versatile plastic resin you might have in many everyday items. Polypropylene, often termed PP, is a thermoplastic polymer belonging to the polyolefin family. Its chemical formula is (C3H6)n, and its molecular structure makes it more challenging than its cousin, polyethylene.
Polypropylene resins showcase excellent properties, making them popular in various industries. To begin with, it’s usually opaque and low-density, with outstanding thermoforming and injection molding characteristics. It performs well within a particular temperature range, maintaining its properties between -20°C and 120°C. Beyond this range, PP can become brittle at colder temperatures and unusable at higher ones.
Polypropylene is not a one-size-fits-all material—you’ll come across different types designed to suit specific applications. For instance, polymers such as the homopolymer and copolymers provide diverse possibilities in industries that require unique solutions.
You’ll find polypropylene in a wide array of products with diverse uses. Thanks to its heat resistance, low density, and durability, it’s an ideal candidate for packaging, automotive parts, textiles, and more. You’ll notice that polypropylene also appears in your average household.
The next time you come across a plastic item, it might be made of polypropylene. Now that you know more about this remarkable resin, don’t hesitate to explore how it benefits various industries and our everyday lives.
- Polyethylene Terephthalate
Polyethylene terephthalate, commonly known as PET or PETE, is a versatile material that belongs to the polyester family of polymers. When encountering plastic products, there’s a good chance you have come across this resin type.
PET is widely used in various applications thanks to its impressive combination of mechanical, thermal, and chemical properties and its dimensional stability.
You will often find it used in beverage and food containers, such as those for soft drinks and other liquids. Even some beer bottles employ PET, utilizing a multilayer structure incorporating layers of polyvinyl alcohol (PVOH) or polyamide (PA) to reduce oxygen permeability and protect the beverage.
PET is also popular in the textile industry, where it’s spun into fibers for permanent-press fabrics.
When recycling it, you might notice that it falls under recycling code “1.” This means that products made with PET are relatively easy to collect, sort, and recycle. PET is highly valued in the recycling process, as it can be turned into many new products, such as fibers for clothing, carpets, or even new containers.
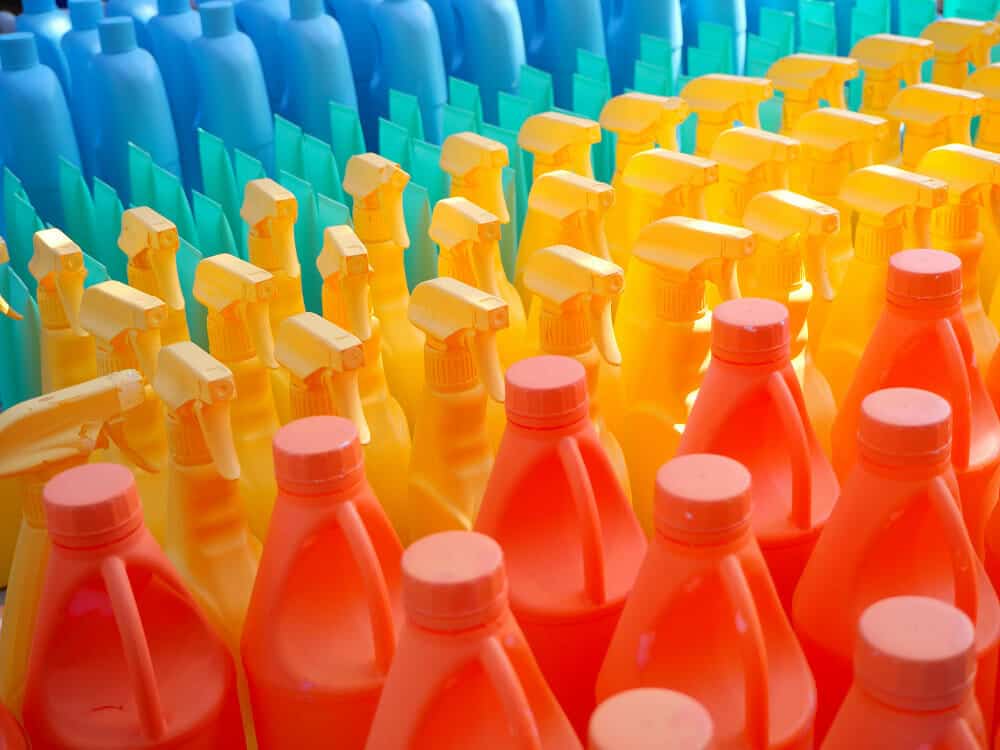
Apart from the aforementioned uses, PET has various applications due to its excellent properties:
- Clarity and strength: Known for its strength and clarity, PET is widely used in packaging materials.
- Lightweight and durable: Products made from PET are often lightweight but still hold up well under stress, making them suitable for daily use.
- Barrier properties: The barrier properties of PET help keep food and beverages fresh, extending their shelf life.
- Polyvinyl Chloride
Polyvinyl chloride, or PVC, is a popular type of plastic resin used in various applications. This versatile material has unique properties that make it suitable for products ranging from pipes to everyday household items. PVC can be categorized into two main types: flexible and rigid.
Flexible PVC has a 1.1-1.35 g/cm³ density and is created by adding compatible plasticizers. These plasticizers reduce the crystallinity and make the material more adaptable to different uses. You’ll find flexible PVC in cables, hoses, or flooring materials.
On the other hand, rigid PVC is a brittle, solid plastic that doesn’t contain plasticizers. It’s commonly used in window frames, pipes, and building siding applications. Rigid PVC is known for its linear solid polymers and structural similarity to polyethylene.
Apart from these broad categories, PVC also comes in other varieties, such as:
- CPVC (Chlorinated PVC) – PVC with added chlorine for improved heat resistance and durability
- PVC-O (Molecularly Oriented PVC) – PVC that is stretched during manufacturing to improve its strength and impact resistance
- PVC-M (Modified PVC) – PVC that has been modified with other materials for improved performance in specific applications
The microstructure of PVC consists of linear polymers that are strong and durable. The monomers are arranged head-to-tail, with alternating chloride and carbon centers. PVC mainly has an atactic stereochemistry, meaning the relative stereochemistry of the chloride centers is random.
In summary, polyvinyl chloride can be found in various forms and serves numerous applications. Whether using its flexible or rigid variation, PVC provides a versatile and durable option for your manufacturing needs. With its diverse range of types, you can find the perfect PVC material to suit your specific requirements.
- Polystyrene
Polystyrene (PS) is a versatile and widely used plastic resin used in various applications. It is a naturally transparent thermoplastic, available in solid form and as a rigid foam material.
You might know polystyrene in the form of styrofoam, often used for insulation and in disposable food containers. This lightweight foam offers excellent insulation properties, making it a popular choice for warming hot and cold drinks.
As a thermoplastic polymer, polystyrene is in a solid, glassy state at room temperature, but it flows if heated above 100°C, known as its glass transition temperature. This characteristic allows it to be easily molded into various shapes and forms. When cooled, it becomes rigid again, maintaining the desired shape.
Among its many uses, polystyrene is perfect for manufacturing disposable cutlery, CD cases, and even toys. Its low melting point and precise, brittle properties make it suitable for the precision molding of small parts and vacuum-forming processes when producing a range of packaging materials.
PS is a versatile plastic resin used in many applications due to its transparent, moldable, and insulating properties. Notable forms like styrofoam highlight its significant role in everyday products and packaging.
- High-Density Polyethylene (HDPE)
HDPE is a popular type of polyethylene known for its high density and crystalline solid structure. As a linear version of polyethylene, it offers impressive strength, rigidity, and resistance to environmental stress cracks.
They are widely found in products like drain pipes, gas pipes, and heavy-duty storage containers such as bottles and trays.
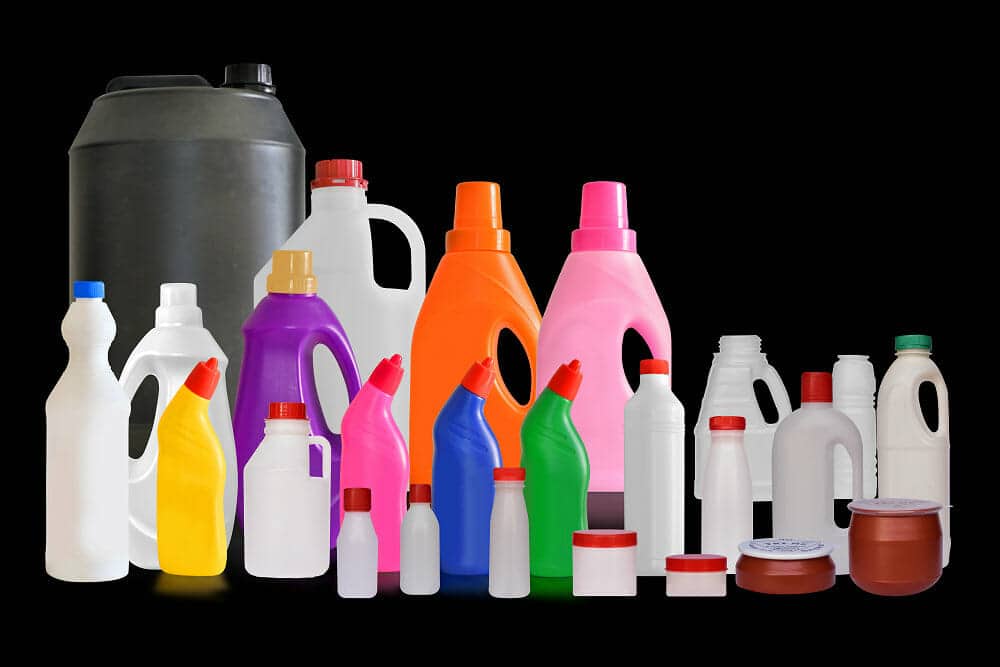
Your everyday encounter with HDPE might include various packaging materials, like milk jugs and detergent bottles. It’s also commonly used in the construction industry for geomembranes and other applications requiring excellent chemical resistance and durability.
- Low-Density Polyethylene (LDPE)
LDPE is another type of polyethylene with a branched structure, which results in a lower density and less crystalline structure than HDPE. As such, LDPE is more flexible and translucent, making it ideal for various applications where flexibility is crucial.
LDPE products can take many forms, including films for food wrapping and packaging or plastic grocery bags. It’s also used to make squeezable bottles and for insulating electrical wires.
Chemical Structures of Resins
You might be curious about the different types of plastic resins and their chemical structures. Let’s dive into some of the most common ones and their mechanisms.
Understanding different plastic resin’s chemical structures and mechanisms will help you make informed choices for your projects. It’s always helpful to consider the properties and applications of each resin type to ensure the best fit for your needs.
Frequently Asked Questions
What are the main categories of plastic resins used in injection molding?
1. PET or PETE (Polyethylene Terephthalate)
2. HDPE (High-Density Polyethylene)
3. PVC (Polyvinyl Chloride)
4. LDPE (Low-Density Polyethylene)
5. PP (Polypropylene)
6. PS (Polystyrene)
7. Ryton & Kynar (and Other)