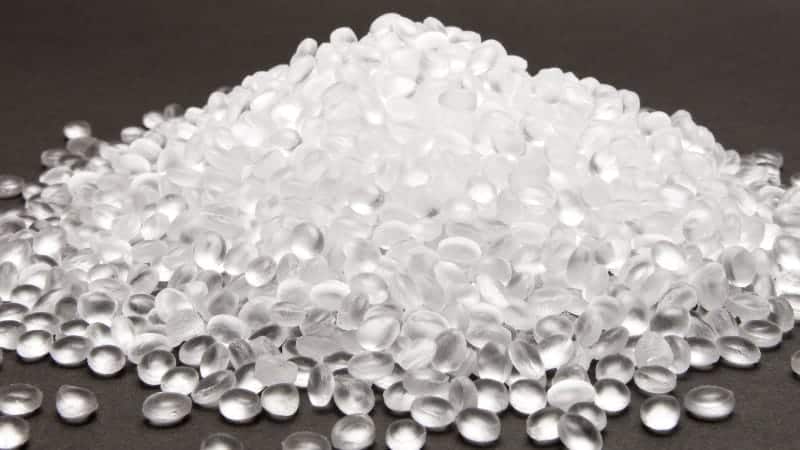
Plastics have become ubiquitous in modern society. Originally developed as inexpensive and versatile substitutes for traditional materials like wood, metal, glass and leather, plastics today are found in everything from household appliances and electronics to clothing, vehicles and construction.
The key property that defines all plastics is their ability to be molded or shaped while soft and then set into a rigid or semi-rigid form. This moldability allows plastics to be manufactured into a huge variety of complex shapes and components in high volumes. Plastics are also very durable, lightweight and corrosion resistant compared to many traditional materials.
Plastics are organic polymers derived mainly from petroleum and natural gas. The basic molecular units, or monomers, are processed and linked together into long chains called polymers. Different types of plastics result from using different monomers or blending them together. Some of the most common plastics include polyethylene, polypropylene, polyvinyl chloride(PVC), polystyrene, nylon and polyethylene terephthalate.
Plastics began being developed commercially in the early 20th century and their use proliferated after World War II as synthetic alternatives to scarce natural resources. Today, plastics have displaced many traditional materials and become essential to modern life, though environmental concerns around plastic waste have also increased. Overall, plastics remain some of the most widely used materials in the world due to their low cost, versatility and performance properties.
Overview of Polyethylene Terephthalate (PET), Polypropylene (PP), and High Density Polyethylene (HDPE)
In this section, you’re going to learn about three popular plastics: Polyethylene Terephthalate (PET), Polypropylene (PP), and High Density Polyethylene (HDPE). These materials are widely used in various industries due to their unique properties and advantages. Let’s explore each one.
Polyethylene Terephthalate is a thermoplastic plastic polymer resin that belongs to the polyester family. It has a glass transition temperature between 67-81 °C and a melting point of 260 °C. PET is widely used in fibers for clothing, disposable beverage or water bottles, and even in combination with glass fiber for engineering resins. Some of its key properties include mechanical, thermal, and chemical resistance, as well as dimensional stability.
Polypropylene is another common thermoplastic polymer that’s known for its versatility. It has a relatively low melting point, around 160 °C, which makes it suitable for a variety of applications. PP is used in packaging materials, automotive parts, and consumer products. Some of its notable characteristics include lightweight, excellent chemical resistance, and the ability to resist fatigue over time.
High Density Polyethylene is a type of polyethylene that’s known for its strength and durability. It’s part of the polyethylene family and has a higher density than other PE varieties, such as low-density polyethylene (LDPE). HDPE is also used in various applications like packaging, construction materials, and automotive components. Its key advantages include excellent impact strength, chemical resistance, and a high strength-to-weight ratio.
Here are a few points to consider when comparing these materials:
- Crystallinity: PET is semi-crystalline, while PP and HDPE are fully crystalline polymers.
- Strength: Both HDPE and PET exhibit high strength, while PP demonstrates moderate strength.
- Temperature resistance: PET has superior thermal insulation compared to PP and HDPE with its higher glass transition temperature.
- Transparency: PET is clear, while PP and HDPE are typically opaque.
- Resistance to degradation: PET is more resistant to photodegradation, while HDPE is less persistent in the environment than PET or PP due to its sensitivity to heat and light.
Manufacturing Process of PET, PP and HDPE

You might be curious about the manufacturing processes of PET (Polyethylene Terephthalate), PP (Polypropylene), and HDPE (High-Density Polyethylene) plastics. Let’s explore how these materials are produced and how they contribute to the manufacturing of plastic bottles and other products.
Polyethylene Terephthalate is widely used in the packaging industry, especially for beverage bottles. The manufacturing process involves four main stages: crystallization, annealing, solid-state polymerization (SSP), and cooling. Traditional Buhler processes integrate these stages to produce PET bottles.
To create PET, you first need to polymerize ethylene glycol and terephthalic acid. Once the process is complete, the result is a polyester resin put through the stages mentioned above, forming the PET we know today.
Polypropylene is another popular plastic used for a variety of purposes. The production of polypropylene involves polymerizing propylene gas with a suitable catalyst, such as Ziegler-Natta-type catalysts. The process yields granules of polymer that can be further processed to create different forms of PP products, such as sheets, films, and fibers.
HDPE is a thermoplastic produced from petroleum byproducts. Its base product is polyethylene (PE), which is polymerized from ethylene in the presence of suitable catalysts like metallocene or Ziegler-Natta-type catalysts. After polymerization, the HDPE is extruded into long filaments which can be used to create various products, such as pipes, containers, and bottles.
The key difference between HDPE and LDPE (Low-Density Polyethylene) lies in the density of the polymer chain. HDPE has fewer side branches, resulting in a higher density and stronger material, making it suitable for more demanding applications.
Use and Application of PET, PP, and HDPE
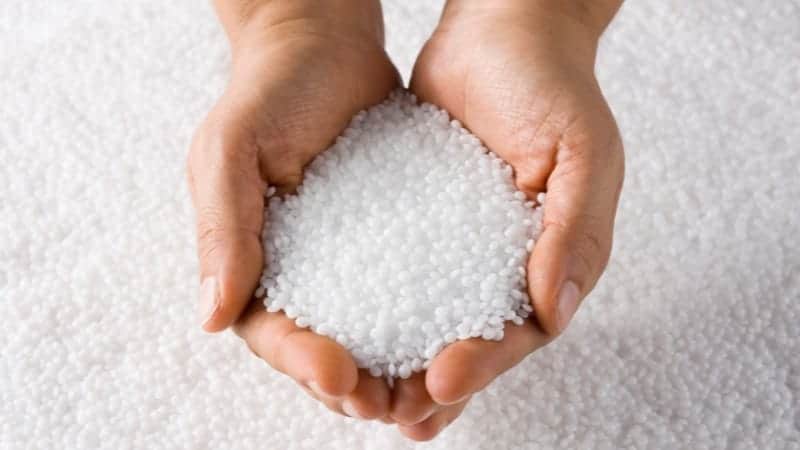
You might be wondering about the various uses and applications of PET (Polyethylene Terephthalate), PP (Polypropylene), and HDPE (High-Density Polyethylene). These materials are widely employed in numerous industries due to their versatile properties and characteristics.
Polyethylene Terephthalate is a popular choice for the packaging industry due to its flexibility, lightweight, and resistance to impact. You will often find containers for food and liquids. Besides packaging, PET is also utilized in textiles and clothing, as it is transformed into fibers. In terms of sustainability, recycled PET (r-PET) and post-consumer recycled (PCR) materials are also available, contributing to the reduction of plastic waste.
Meanwhile, Polypropylene is appreciated for its stiffness and heat resistance, making it ideal for hot food containers and microwave-safe packaging. PP can be found in various applications, such as agricultural products and even in the fabric for sportswear. As a material with high tensile strength, it is also employed in engineering plastics. PP is recyclable which helps in waste management.
High-Density Polyethylene is another versatile plastic material commonly used in everyday items. Its high density makes it robust and resistant to moisture and impacts. HDPE is often found in packaging applications, such as containers, detergent bottles, and plastic waste bins. Additionally, it is employed in the automotive and agricultural sectors, providing excellent performance and durability. Like PET and PP, HDPE can also be recycled, reducing its environmental impact.
Effects on Environment: Recycling and Waste Management
Recycling, plastic packaging waste, and waste management strategies have a significant impact on the environment. When it comes to polyethylene terephthalate, PP, and HDPE, recycling can help mitigate their detrimental effects on our planet.
You might be curious about how these substances can degrade. Polystyrene, a common component of plastics, experiences weathering. This process breaks the material down into smaller pieces or oligomers which can accumulate in the environment. These tiny fragments can persist for a long time, leading to ingestion by wildlife and even entering the human food chain.
Landfills and Disposal
When it comes to the disposal of PET, PP, and HDPE, putting them in landfills is one method used. However, this approach poses environmental risks. Chemicals can seep into groundwater systems, and non-degradable plastics like PET tend to accumulate and take up valuable land space. To minimize these impacts, more sustainable waste management practices, such as recycling, are advisable.
Sustainability and Recycling
Recycling offers a more sustainable solution for managing PET, PP, and HDPE plastic waste. By reusing these materials, you can help minimize landfills, reduce the extraction of virgin raw materials, and lower the energy requirements for manufacturing new plastics. Not only does recycling cut down on carbon dioxide emissions, but it also helps promote greener, more eco-friendly practices across the board.
As part of your waste management efforts, you can also consider alternatives such as composting. When you compost biodegradable plastic materials, breaking them down into organic matter, you contribute to environmental sustainability by reducing carbon emissions and providing valuable nutrients to the soil.
Analysis Techniques: Assessment and Validation of PET, PP and HDPE
In your quest to study and comprehend PET (Polyethylene Terephthalate), PP (Polypropylene), and HDPE (High Density Polyethylene) plastics, it’s essential for you to acquaint yourself with a variety of analysis techniques that could aid in the assessment and validation of these plastics.
One valuable technique to consider is scanning electron microscopy (SEM). With this method, you can gain insight into the surface and compositional information of the plastics. SEM allows you to examine the fine structures, microstructures, and morphology of PET, PP, and HDPE samples.
Similarly, differential scanning calorimetry (DSC) is another useful technique for plastics analysis. By measuring the heat flow associated with transitions and reactions, DSC can determine the melting and crystallization temperatures of PET, PP, and HDPE. This knowledge could help you understand how these plastics behave under various conditions.
Aside from physical properties, it’s crucial to analyze the market aspects of PET, PP, and HDPE. For instance, the annual production and distribution of these plastics can provide insights into the overall market trends and growth patterns. Pay attention to the compound annual growth rate (CAGR) to gauge the future potential and sustainability of each plastic.
Focus on the characteristics of each plastic as well. For example, PET, PP, and HDPE might be found in different forms, such as fibres or solid materials. Analyzing these can help determine the optimal use cases for each type of plastic.
When investigating the chemical structure and composition of PET, PP, and HDPE, techniques such as Fourier-transform infrared spectroscopy (FTIR) are often employed. By analyzing the spectra generated through FTIR, you can identify different functional groups and classify the plastics based on the spectral information.
Frequently Asked Questions
What are the common applications of HDPE, PET, and PP?
HDPE has various applications including containers, bottles, grocery and trash bags, and pipes for water and gas. PET is used in making water and soda bottles, food packaging, textile fibers, and electronic components. PP is utilized for plastic bottles, food containers, automotive parts, and packaging materials.
How do the mechanical properties of PET and PP compare?
PET has excellent chemical, mechanical, and thermal resistance properties, as well as dimensional stability. It can be semi-rigid to rigid depending on how it is processed. PP, on the other hand, is known for its flexibility, impact resistance, and fatigue resistance. It is also resistant to temperature and chemical exposure.
Which is more chemically resistant: HDPE or PP?
Both HDPE and PP are chemically resistant plastics, but their specific resistance to different chemicals may vary. HDPE is resistant to most acids, bases, and organic solvents, while PP has an even broader chemical resistance, including against strong acids and bases.
What are the recycling codes for HDPE, PET, and PP?
The recycling codes for these plastics are as follows: HDPE is assigned with recycling code #2, PET is associated with code #1, and PP uses code #5.
Are PET and HDPE plastics safe for food packaging?
Yes, both PET and HDPE are considered safe for food packaging. They are approved by authorities like the FDA and the European Food Safety Authority for contact with food. These plastics don’t leach harmful substances into the food, thus ensuring safety and quality.
How do the costs of HDPE, PET, and PP vary?
HDPE is a low-price commodity material, with virgin material priced around $8.50 per kg and recycled material at around $2.50 per kg. PET is also a low-price material. The costs of PP depend on the specific grade and application, but it is generally considered a cost-effective material in comparison to other plastics.