
Plastisols are a type of polymer material that has many applications in industry and manufacturing. However, for those unfamiliar with the term, questions may arise around exactly what a plastisol is and how it is used. This article aims to provide a clear explanation of plastisols by defining what they are made of and how their unique properties make them well-suited for certain applications. We will explore the basic composition and characteristics of plastisols and discuss some common uses of this versatile material.
Understanding Plastisol
Plastisol is a unique material that combines polymer particles and a liquid plasticizer to create versatile applications. In this section, you’ll learn about its basic composition and the properties that make it widely used in various industries.
Basics of Plastisol
Plastisol mainly consists of polyvinyl chloride (PVC) particles suspended in a liquid plasticizer, sometimes including small amounts of stabilizers, pigments, and fillers. This blend forms a plasticizing compound that remains fluid at room temperature but can be transformed into a durable solid when heated. Here’s a simple breakdown:
- Polymer Particles: Often, these are PVC or similar polymers.
- PVC is a type of synthetic plastic polymer.
- PVC resin refers to polyvinyl chloride resin, which is a plastic polymer made from the polymerization of vinyl chloride monomers
- Liquid Plasticizer: This gives plastisol its flexibility and fluidity.
- When heated, it interacts with the PVC particles.
This combination is key to plastisol’s functionality, providing a flexible material when cool that solidifies with heat.
Plastisol Properties
One of the most remarkable features of plastisol is how it changes state with heat:
- At Room Temperature: It maintains a liquid state that is easy to work with.
- Upon Heating: It reaches a state where the polymer particles swell, absorb the plasticizer, and fuse, forming a solid material.
Due to these properties, plastisol is suitable for a wide range of applications, from coatings and inks to molds and textiles. Here are some specific characteristics:
- Durability: It forms a tough, wear-resistant surface.
- Versatility: Can be used in a range of products, including outdoor furniture and automotive applications.
- Processability: Can be easily molded or coated onto surfaces before being cured.
Plastisol Applications
Plastisol is a versatile material you’ll find across various industries, thanks to its adaptability, durability, and cost-effectiveness. Whether it’s creating protective coatings or decorating materials, plastisol’s unique properties are tapped into for a wide range of applications.
Industrial Uses
Dip Coating: One of the primary industrial applications of plastisol is dip coating. This process involves submerging a product into a liquid plastisol which then fuses into a solid protective layer upon heating. You’ll often see this technique applied in:
- Tool Handles: For improved grip and insulation.
- Electrical Components: To insulate wires and connectors.
Automotive: In the automotive industry, plastisol serves as a protective coating for parts exposed to extreme conditions. It can be found in:
- Underbody Coatings: Protecting against rust and damage.
- Seals and Gaskets: Providing flexibility and weather resistance.
Medical: Plastisol’s non-reactivity makes it suitable for certain medical tools and components, such as:
- Tubing: Where a flexible, yet durable, coating is required.
- Grip Covers: To enhance grip on various medical devices.
Consumer Products
Screen Printing: When it comes to applying designs to your dark fabrics, plastisol is a reliable textile ink for screen printing.
Plastisol Ink: It is a cheaper ink that has long been the industry standard for screen printing. Plastisol ink is made with polyvinyl chloride (PVC) and plasticizers. It does not contain solvents like other inks.
Screen Printing ensures vivid colors and enduring designs, particularly notable in:
Garment:
- T-shirts: Allowing for vibrant prints that withstand numerous washes.
- Dark Fabrics: Where it’s opacity ensures bright representation of colors.
Playground Equipment: The safety and durability aspects of plastisol come into play in the production of children’s playground equipment. Its application results in:
- Soft Surfaces: To prevent injuries.
- Weatherproof Coatings: To resist sun and rain damage.
When you interact with various products in your everyday life, it’s likely you’re coming into contact with items that have been enhanced or protected by plastisol without even realizing it.
Manufacturing Processes
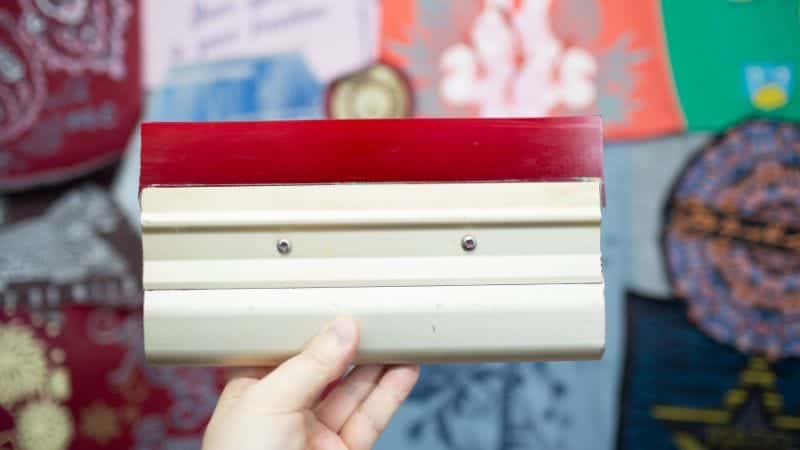
When you delve into manufacturing plastisol products, the procedures can be quite diverse. From applying heat to solidify the material, to shaping and coating the final product, the manufacturing of plastisol involves several key techniques across different processes.
Curing Methods
Curing is a vital process where the liquid plastisol transforms into a tough, permanently set material. This occurs using an oven where plastisol is exposed to high temperatures. The heat level and duration must be precise to ensure proper cure without degrading the material. The thickness of the plastisol plays a crucial role in determining curing time. Typically:
- Thin coatings might cure in minutes.
- Thicker molds could take much longer.
Molding Techniques
In the realm of plastisol molding, you’ll encounter a few techniques:
Slush Molding
A method that fills a heated metal mold with liquid plastisol and then inverts the mold to allow excess material to flow out. This process is often used for hollow products and allows for varying thicknesses in the final piece.
Injection Molding
Not commonly used for plastisol, injection molding is more complex. It involves injecting heated material into a mold where it cools and solidifies.
Rotational Molding
For creating large, hollow items, rotational molding is your go-to. The mold rotates on two axes during curing, ensuring an even coating of plastisol within the mold.
Coating Procedures
Coating procedures can give your product a durable, functional, or aesthetic surface layer.
Dip Coating
In precision dip coating, a part is submerged in plastisol and then removed at a consistent rate to ensure a uniform coating thickness. It’s a straightforward yet effective method to coat products.
Spray Coating
Alternatively, spray coating can be used where a fine mist of plastisol is applied over the object. This method can offer a more controlled application over complex shapes.
By understanding these processes, you can make informed decisions about the manufacturing techniques most suitable for your plastisol product needs.
Physical and Chemical Characteristics
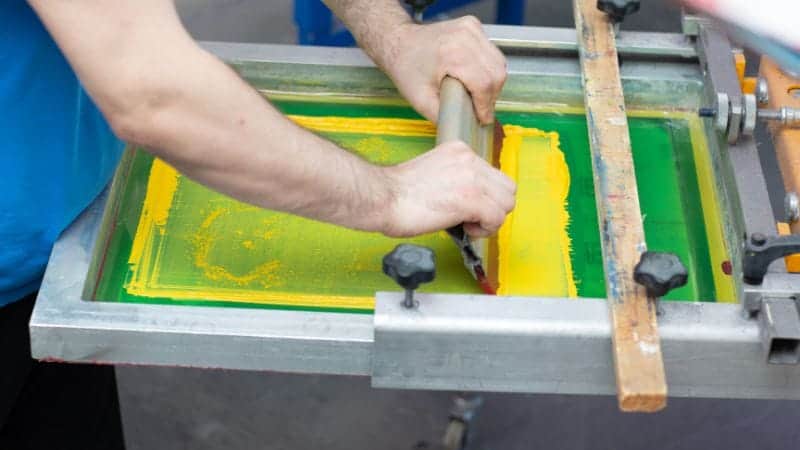
Your exploration into plastisols will reveal that they are not just versatile but also exhibit a range of intriguing physical and chemical properties. Their flexibility and durability are particularly noteworthy.
Rheology and Viscosity
You will find that the rheology of plastisols, or how they flow, is quite fascinating. Initially, plastisols exhibit a low viscosity, making them easy to work with; they can be poured and coated onto surfaces smoothly. Upon heating, as the PVC particles absorb plasticizers, the viscosity increases significantly, resulting in a harder final product. This transformability allows you to control the final hardness of the product through thermal processes.
Electrical and Chemical Resistance
Plastisols are known for their excellent chemical resistance. This means that the materials they coat are protected against various chemicals, which extends the lifetime of the product. Their dielectric strength also makes them an excellent choice for electrical insulation. The flexible nature of cured plastisol coatings, combined with this durability, provides a reliable protective barrier in a wide array of applications.
Advancements and Considerations
Exploring the latest in plastisol technology, you’ll find innovative applications that extend its utility, as well as increasing attention to environmental and safety considerations. Let’s delve into the advancements and critical factors that shape the current landscape of plastisol use.
Innovative Uses and Technologies
Plastisol has witnessed a variety of innovative applications, thanks to advancements in technology. You may now encounter plastisol in:
- Medical Devices: Utilization of non-phthalate plastisol for improved safety in medical applications.
- Automotive Parts: Enhanced as a flame retardant material for increased safety in vehicle components.
The incorporation of sustainable materials has led to the development of eco-friendly plastisol options which aim for a reduced environmental impact without sacrificing quality.
Environmental and Safety Factors
Your health and the environment are paramount, thus recent formulations of plastisol seek to minimize potential risks. Important aspects include:
- Phthalates Reduction: The trend is shifting towards phthalate-free plastisols to mitigate health concerns.
- BSR (Buzz, Squeak, and Rattle) Reduction: Advancements in plastisol applications have led to quieter products that contribute to improved safety and experience.
With the focus on sustainability, manufacturers strive for:
- Recycling Efforts: Increasing the recyclability of products containing plastisol.
- Reduced Waste: Efforts to minimize waste in the production process of plastisol.
Each of these considerations plays a part in pushing plastisol into a more environmentally friendly and safer future.
In summary, plastisols are a suspension of PVC particles in a plasticizer that remains liquid at room temperature until heat is applied. This allows for easy application and adhesion to various substrates. Their ability to be printed, coated, or molded make plastisols useful for a wide range of industrial and commercial products and components. As long as the proper plasticizers are selected to maintain flexibility or rigidity as needed, plastisols offer manufacturers and fabricators a cost-effective and durable material option.